A Biased View of Welding Inspection
Table of ContentsWelding Inspection - TruthsLittle Known Questions About Welding Inspection.5 Easy Facts About Welding Inspection ShownExamine This Report about Welding InspectionGetting The Welding Inspection To Work
This technique is done in a workshop or area while the welding is being done. The important things that are visually checked include the welder's certification, slag elimination, joint prep work, weather condition problems, existing made use of, and condition of the electrode. 2- Magnetic Fragment Checking This examination is used to discover any type of surface area or hardly subsurface issues in a weld.Bits of iron are then related to the magnetic area and if there are any type of issues, the particles of iron will certainly develop around the issue, which shows where the defect is and also why it happened. 3 Liquid-Penetrant Testing This test will find issues in the surface of the weld like porosity and hairline splits.
A designer is after that applied that will certainly reveal if any kind of defects are visible. 4 Ultrasonic Checking This test is achieved by the use sound resonances, which are then transmitted through the welded joint. The signals gotten on a glass screen will figure out if there are any kind of flaws in the joint of the weld.
5 Eddy Current Testing This examination will show incredibly little splits and also is completed by the use of a circular coil that carries rotating currents, which is placed near the weld. The alternating currents will develop an electromagnetic field, which will certainly interact with the weld as well as subsequently, produce an eddy current.
9 Easy Facts About Welding Inspection Described
The resulting impression size is referred to as a solidity gauging table. 8 Devastating Testing This examination is a harmful examination that is accomplished by reducing the completed weld right into pieces, this is per the code for root bend, face bend, tensile examination, and also side bend. It is used to situate slag addition, porosity, as well as undercutting flaws in welds as well as is really effective.
It's likewise not useful for a person that is not skilled in the essential treatments to do this job. Analysis of weld features includes the size of the weld and also the existence of suspensions. The dimension of a weld can be incredibly vital, as it commonly correlates straight to strength as well as linked performance - Welding Inspection.
Uncovering weld stoppages additionally is necessary due to the fact that flaws within or surrounding the weld, depending on their size or place, might protect against the weld from fulfilling its intended function. When interruptions are an inappropriate size or in an unacceptable area, they are called welding problems, and they can create early weld failure by reducing toughness or creating anxiety concentrations within the bonded element.
It is essential to choose a welding standard intended for use within the particular market or application in which you are involved. Weld Examiner Responsibilities Welding evaluation calls for an understanding of weld drawings, signs, joint design, treatments, code and typical demands, and also evaluation and also screening strategies. Because of this, many welding codes as well as standards need that the welding inspector be officially qualified, or have the necessary expertise and experience to perform the evaluation.
The Only Guide to Welding Inspection
Right here are a few points that a welding assessor should understand and Visit This Link also tasks he ought to have the ability to do: Particular treatments must be complied with to certify welders as well as welding treatments. The certification procedure is an important part of the overall welding quality system, and also the welding examiner often is required to collaborate and also verify these kinds of credentials examinations.
These welded samples usually are needed to be evaluated after completion. Radiographic, microetching, directed bends, transverse tension, and nick-break crack are several of the tests that are used. The examination results have to satisfy or exceed the minimum needs as specified in the welding code or requirement before the treatment can be qualified.
The welding inspector have to be qualified of determining all of the various welding suspensions throughout visual inspection. Welding Inspection. He additionally should be able to review, in terms of the relevant welding code or requirement, the importance of recognized interruptions to identify whether to accept or deny them during screening and manufacturing.
A welding examiner sometimes is called for to carry out weld testing by surface area crack discovery techniques. He also might have to assess the test outcomes of these testing approaches. The inspector should comprehend testing methods, such as liquid penetrant and magnetic particle inspection. In addition, he needs to understand exactly how the examinations are made use of and what they will find.
The Buzz on Welding Inspection
These evaluation techniques are made use of to examine the interior structure of the weld to develop the weld's honesty, without destroying the welded component. The welding inspector may be called for to understand this sort of screening and also be skilled in the interpretation of the outcomes. Radiographic and also ultrasonic weld inspection are both most typical approaches of NDT made use of to spot discontinuities within the internal framework of welds.
Radiographic screening makes usage of X-rays produced by an X-ray tube or gamma rays produced by a contaminated isotope. The standard principle of radiographic evaluation is the same as that for medical radiography. Passing through radiation is gone through a strong item, in this situation a weld, onto a photographic film, resulting in a picture of the item's interior structure.
Blemishes within or nearby the weld might avoid the weld from meeting its designated function. Locations of the weld where the density has actually been transformed by gaps, such as porosity or fractures, will certainly show up as dark outlines on the check this movie.
All stoppages are spotted by checking out form and also variation in thickness of the refined movie. Ultrasonic screening utilizes mechanical vibrations similar to seem waves but of higher regularity. A light beam of ultrasonic power is routed right into the weld to be examined. This light beam takes a trip through the weld with insignificant loss, except when it is obstructed and reflected by a stoppage.
Welding Inspection Things To Know Before You Buy
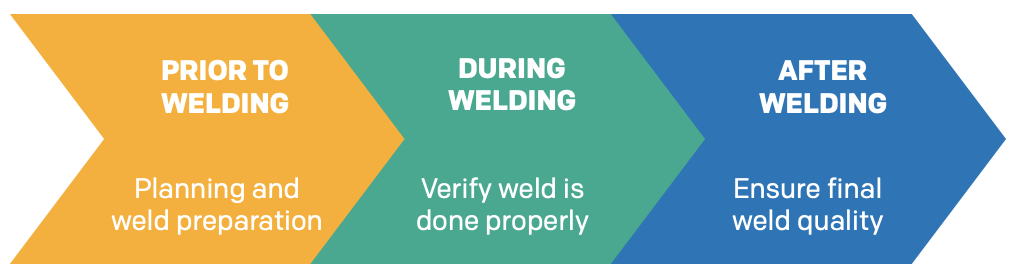

These examinations are made use of during welding procedure or welder efficiency certification testing. The welding assessor should be experienced in the ability to review engineering and also manufacturing illustrations, and be able to translate all information as well as symbols that give information regarding the welding requirements.
You have to hold this level for a minimum of 2 years prior to moving to the next level. You have to hold the CSWIP welding inspector degree for a minimum of two years before relocating to the following degree.